- Through the visual representation of abandoned spaces, artifacts of history are at once fresh and new, ancient and decayed. The past continues to live in these forsaken, ruined, or empty spaces and we ask.
- A lack of space often forces us to look for a small corner to set up a makeshift workspace. Whatever your situation might be, remember that you can always create an original and very practical desk space. And to prove it, we have examples to show you. Our list of original desk spaces 1.
- Along with Goldstone, these happiness crystals rock at harnessing personal power and renewing your zest for life. The Bedroom The place of romantic love, restorative sleep, and peaceful contemplation, the bedroom is an excellent room for heart chakra stones like Aventurine and Jade, which attract love by stimulating and balancing the heart chakra.
- The default single blog post design has a center layout with a subscription form on the right and the social media sharing option on the left. Lots of white space is used in this template to give a roomy feeling and also to make the user interactions easier. Those who are planning to revamp their existing blog will find this template useful.
- Personal Collectionempty Spaces The Blog Example
- Personal Collectionempty Spaces The Blogs
- Personal Collectionempty Spaces The Blog Examples
A mirror and ornaments can fill empty spaces too. Put a mirror against a wall, with ornaments next to it, to fill an awkward empty space. This will look aesthetically pleasing and bring the entire space together. Use any one of the five decorating tips above to make your empty spaces look less awkward using timeless decor styles.
Solving the ‘Nothing I Need is Ever There’ Dilemma – Step 2
In Step 1 we talked about determining the state of your lab and figuring out how to take the first steps toward making availability of lab supplies less frustrating and less costly. Need a refresher? Check out Solving the ‘Nothing I Need is Ever There Dilemma – Step 1.
Want to know the secret to solving this dilemma? It’s figuring out what you need to order, how much and when.
Wait… what? I’ll bet you’re thinking to yourself, “that’s not the solution, that’s my problem!!” Exactly. Let’s figure this out starting with the people who use the lab supplies you manage. Are they the kind of people who let other people know when the shelf is empty? Or, better yet, when supplies are starting to run low?
Or, is it more likely that the shelf will sit empty while everyone just orders their own supplies?
Personal Collectionempty Spaces The Blog Example
If the latter, you’ll need a process to review or count what’s on the shelf on a regular basis. If the former, you might be able to manage your stockroom or lab with an alert type process. Either of these processes can be done manually or using digital tools.
Exploring manual options
There are a few manual options available for alert processes. These include:
- White board, clip board or sticky notes – users write the item or items that need to be ordered and how many. The person managing the stockroom determines the final order quantities after reviewing the white board/sticky notes.
- Visual Signal (sometimes called a two bin or Kanban) system – the stockroom manager places a visual indicator within the stock on a shelf. When users see that visual indicator – often a colored card or a card with ordering information – the user either takes that card to person who orders for that stockroom or places the card in a basket to be collected.
It’s often easier to change your process versus trying to change human behavior. If you know your stockroom users are unlikely to let you know when the shelf is running low on an item, a review/count process may be more effective than an alert process. Your best bet is to establish time to do periodic cycle counts. With manual periodic stock counts, the stockroom manager counts each item in the stockroom. The counts are recorded using pen and paper, spreadsheet or another document.
- The stock count process can either focus on counting the empty spaces or on counting the items remaining on the shelf.
- Counting empty spaces creates orders that fill the shelf.
- Counts of items remaining on the shelf are compared to pre-established reorder points. This type of stock count is an important tool for optimizing spend, shelf space, and availability of supplies. We’ll cover this topic in more detail in a future article.
- Frequency of counting depends on how much shelf space you have and how many supplies are used each day. Start by doing counts a few times a week and gauge the frequency you need at your site from there.
Items to be ordered – either from the stock counts or the alert system – are then entered into an ordering system or sent/called into each vendor.
The pros of using a manual system are that it’s easy to set up and it can be effective. However, manual systems are often tedious, cumbersome, and time consuming both for counting items and placing orders.
Digital options can boost efficiency
The digital options for both count processes follow the same general flow as the manual options, but leverage a variety of digital tools to complete these steps.
For an alert type process, some inventory management programs offer mobile apps for recording items as they are taken. The process is as simple as scanning the bar/QR code on the product shelf and indicating quantity taken. You are alerted to reorder when the quantity on your shelf falls below a pre-set reorder point.
Another efficient source of digital alerts is your Laboratory Information Management System (LIMS). These systems track and associate the reagents and consumables that are used with each experiment. They can also provide you with dashboards to track stock levels and notify you when you are getting low to trigger a reorder.
Digital inventory management systems also streamline counting stock – often reducing the time need to count stock by up to 50% and with fewer errors. To count, you scan the bar/QR code on the shelf, enter the count of items on the shelf, and continue until all items are counted.
In more advanced inventory management solutions, like the one offered by Thermo Fisher Scientific, the system both automatically calculates the order quantity needed and places the order directly with the vendor. This dramatically reduces the time to identify and order supplies needed by the lab.
Digital inventory management systems take a little longer to set up, but quickly return that initial investment through more efficient and more accurate stock counting and ordering.
Your next steps? Assessing which of these options makes the most sense for you and your lab.
Next up for us? Taking a more detailed look at some best practices in tactical inventory management.
Top 5 Connected Lab Blogs for 2020
Here are the five most read articles on the Connected Lab bl...
Read MoreLaboratory Inventory Management Tips
Solving the ‘Nothing I Need is Ever There’ Dilem...
Read MoreEssential Details for Successful LIMS Implementation Projects
...
Read MoreAs a reader of this blog, you know that different workloads need different storage – a high-performance transactional system like a stock-trading platform needs a different storage solution than an archival backup system.
Software-defined storage solutions like Microsoft’s Storage Spaces Direct, deliver innovative technology to pool and manage storage devices directly connected to servers. Though that alone might have seemed like magic a few years ago, it doesn’t include enough magic to overcome matching a workload to the wrong storage configuration. You wouldn’t expect a go-kart engine to power your race car, and storage is no different.
In this blog series I will be sharing some helpful, broad guidelines to optimize your Storage Spaces Direct configuration based on our workload testing. I will be sharing early results and recommendations based on various configurations running different types of workloads.
This first blog is an introduction to workloads and I/O patterns.
Storage Spaces Direct, Meet Workloads and I/O Patterns
Consider two common database workloads, data analytics and transactional processing. Data analytics, as well business intelligence and data warehouse, are read-intensive and perform large block I/O.

Table 1 reports the read I/O from a SQL Server Data Warehouse Fast Track validation test, which is similar to the TPC-H benchmark. 25.03% of reads were 1,024 KB, 7.69% were 968 KB, 3.30% were 960 KB, etc. Data analytics issues lots of big-block reads.
Table 2 reports the read I/O from SQL Server during Hybrid Transactional/Analytical Processing (HTAP), where transactional processing dominates the occasional analytics query. As you browse through the product catalog in an online store, 99.99% of reads are 64KB; not shown are the writes issued when you place an order, but those are 64KB or less as well. Transactional systems issue lots of small-block reads (and writes).
Hyperconverged Infrastructure, meet the I/O Blender Effect

Hyperconverged infrastructure (HCI) is often associated with software-defined storage: the server running applications – typically virtualized applications – is also providing the software-defined storage. We previously demonstrated that as you add virtualized applications to the server, the server quickly hits a storage performance bottleneck that effectively limits the number of workloads that server can support – workload density.
This is caused by the I/O Blender Effect. Consider the data analytics workload above, which issues many large-block reads. Virtualize that workload, and several more like it, and run those on an HCI server. Although each workload issues sequential reads, those reads are intermingled with the reads from all the other virtualized workloads. At the hypervisor and storage level, all that I/O gets mixed up – as if it were run through a blender. The storage system gets random I/O, even though it started off as sequential I/O.
If you also move some transactional workloads with their small-block reads and writes to that same server, that will magnify the I/O Blender Effect: the storage system gets intermingled small-block writes with large-block reads. That’s stressful both for hard disk drives (HDDs) due to increased read/write head movement, and for solid state drives (SSDs) due to the added complexity being handled by the SSD firmware. In both cases, “stressful” workloads cause increased latency, slowing I/O request completion, slowing down applications and challenging your service level agreements (SLAs).
Optimize Your Storage Spaces Direct Configuration By Matching it to Your Workload
Storage Spaces Direct supports a variety of storage configurations, combining SSDs and HDDs to meet your workloads’ storage performance needs, as shown in Table 3.
If you need blazing performance, you can use NVMe™ drives with SAS or SATA SSDs. If you need high capacity at low cost, you can use a few SSDs with many HDDs. For something in the middle, you can choose from several additional configurations.
Personal Collectionempty Spaces The Blogs
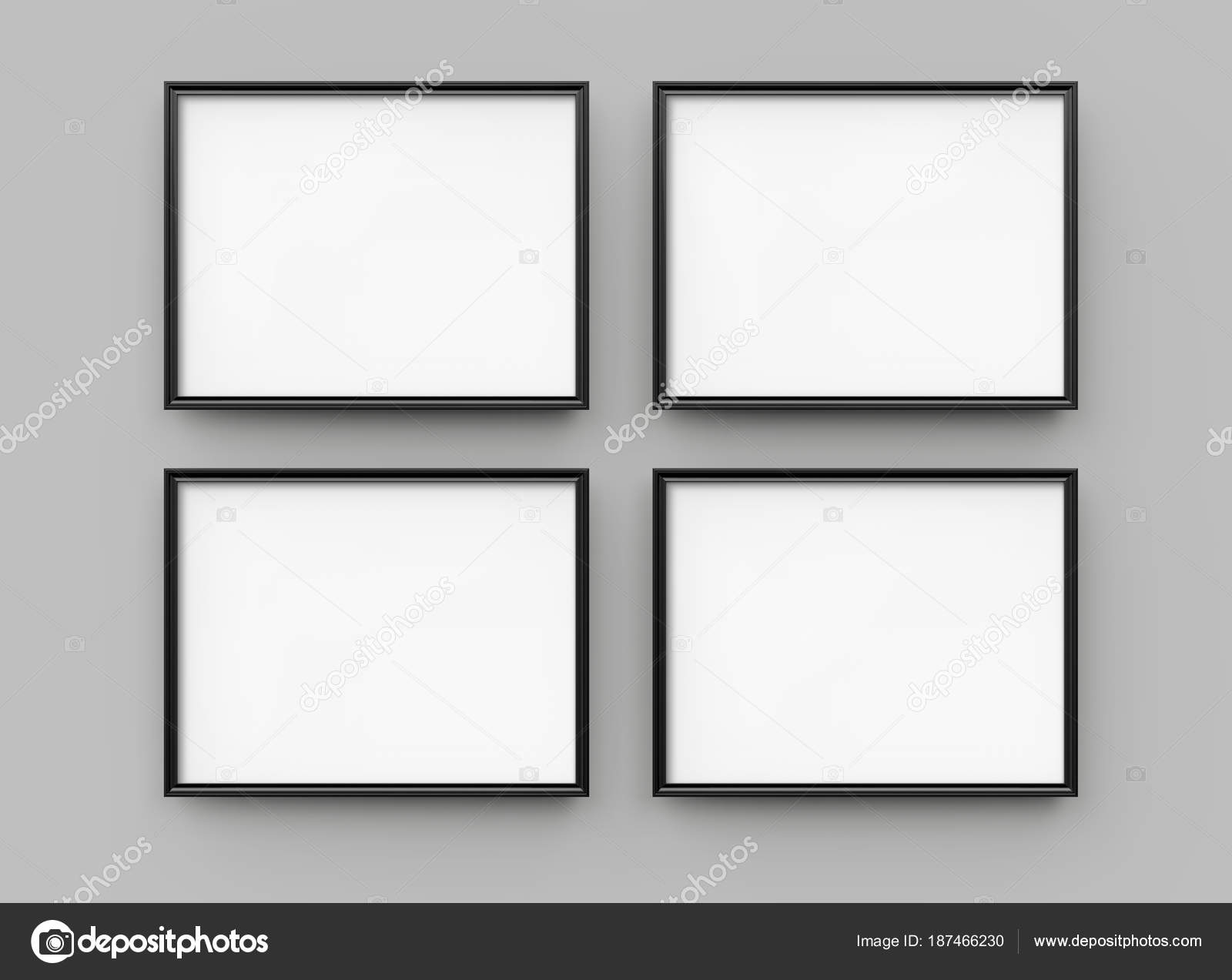
That’s Great, But Which Should You Choose, And Why?
Personal Collectionempty Spaces The Blog Examples
That’s a great question, with a complex answer – because every workload is different, so the perfect matching storage configuration will be unique. But that’s not a very helpful answer 🙂
There are actually more combinations than Table 3 indicates. To start with, HDDs and SSDs are available as both SAS and SATA. As well, Western Digital’s product portfolio includes multiple HDD product families that are helium- or air-filled at different capacities and price points, and multiple SAS SSD product families with different endurance (DW/D) and price points.
Too much complexity! Too many permutations! How do I choose?!
Western Digital’s Data Propulsion Labs™ team is testing many different Storage Spaces Direct configurations, and based on some early results we can get you started with some broad guidance on how to best power your enterprise applications and Big Data and Fast Data initiatives. We’ll continue provide additional guidance as additional testing is completed and new products in our portfolio are released.
In my next blog, I will share our first testing results and some initial guidance for different type of workloads.
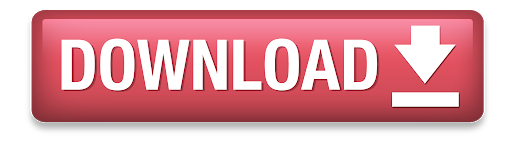